Essential Precautions for Battery Safety in Electronic Systems and Equipment Maintenance
6/26/20247 min read
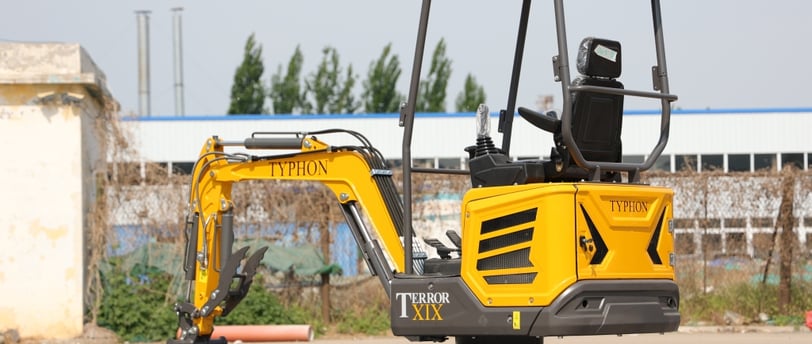
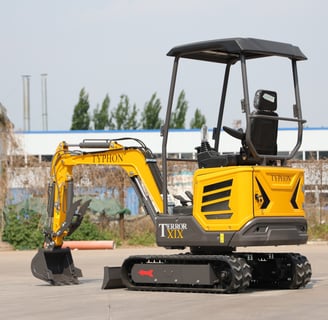
Importance of Disconnecting the Battery Line Before Electronic System Operation or Welding
When working with electronic systems and performing maintenance tasks such as welding, it is imperative to disconnect the battery line beforehand. This precautionary measure is crucial for ensuring the safety of both the individual performing the task and the integrity of the equipment. By isolating the power source, the risk of electric shock and accidental short circuits is significantly reduced. Moreover, it prevents potential damage to sensitive electronic components that could be caused by electrical surges or spikes during operation.
The proper procedure for disconnecting the battery involves a systematic approach. Begin by turning off the ignition and removing the keys from the vehicle or device. This step is essential to ensure that no power is being drawn from the battery. Next, locate the battery terminals, which are typically marked with a positive (+) and a negative (-) sign. Using an appropriate wrench or socket, loosen the nut on the negative battery cable first. Carefully detach the negative cable and secure it away from the battery to prevent accidental reconnection.
Once the negative cable is disconnected, proceed to loosen and remove the positive battery cable. It is crucial to follow this sequence—disconnecting the negative cable first and reconnecting it last—to minimize the risk of creating a short circuit. When reconnecting the battery, attach the positive cable first and then the negative cable. This ensures that the battery is safely reconnected without generating sparks or causing electrical interference.
Failure to disconnect the battery line before commencing electronic system operations or welding can lead to severe consequences. Potential hazards include electrical shocks, which pose a significant risk to personal safety, and the possibility of causing permanent damage to the electronic system. Additionally, welding activities can generate electromagnetic fields and heat, which might interfere with the functionality of the electronics if the battery remains connected. Therefore, adhering to this safety protocol is essential for preventing accidents and maintaining the reliability of electronic systems.
Step-by-Step Guide to Safe Battery Disconnection and Reconnection
Ensuring the safe disconnection and reconnection of a battery is a critical aspect of maintaining electronic systems and equipment. Following a structured approach minimizes the risk of accidents such as sparks or short circuits, which can result in severe damage. This guide provides detailed steps to ensure safety and efficiency.
First, gather the necessary tools: insulated gloves, safety goggles, a wrench set, and a voltage tester. These tools are essential for protecting yourself and ensuring that the battery is handled correctly. Before beginning, ensure that the electronic system or equipment is turned off to prevent any accidental electrical discharge.
The first step in the disconnection process is to identify the battery terminals. Typically, batteries have a positive terminal (marked with a "+" sign) and a negative terminal (marked with a "-" sign). Using the appropriate wrench, carefully loosen the nut on the negative terminal first and remove the negative cable. This is crucial as disconnecting the negative terminal first reduces the risk of creating a short circuit. Repeat the process for the positive terminal.
Once both cables are disconnected, inspect the battery and terminals for any signs of corrosion or damage. Clean the terminals using a mixture of baking soda and water if necessary, and ensure that they are completely dry before proceeding.
To reconnect the battery, reverse the disconnection steps. Attach the positive cable to the positive terminal first and secure it tightly with the wrench. Then, connect the negative cable to the negative terminal and ensure it is firmly in place. Always connect the positive terminal before the negative to avoid potential sparks or short circuits.
After reconnecting the battery, double-check all connections to ensure they are secure. Use the voltage tester to confirm the battery's voltage is within the expected range, indicating a proper connection. Finally, turn on the electronic system or equipment to verify that it is functioning correctly.
By following these meticulous steps, you can safely disconnect and reconnect a battery, ensuring the longevity and reliability of your electronic systems and equipment.
Safety Measures When Using Battery Charging Lines
Ensuring safety when using battery charging lines is paramount to prevent accidents and equipment damage. One of the most crucial precautions involves carefully handling the positive (+) and negative (-) clamps. It's essential never to touch these clamps simultaneously or allow them to contact the mini-excavator or any other part of the equipment. This precaution is vital to avoid short circuits, which can lead to severe injuries or equipment failure.
When working with battery charging lines, always ensure that the equipment is turned off and disconnected from any power source before attaching the clamps. This step minimizes the risk of electrical shock or burns. Additionally, use insulated tools and wear appropriate personal protective equipment (PPE) such as gloves and safety glasses to protect yourself from potential hazards.
The clamps should be connected in a specific order to maintain safety. Start by attaching the positive (+) clamp to the positive terminal of the battery. Ensure a secure connection to prevent slipping or accidental contact with other metal parts. Next, attach the negative (-) clamp to a metal part of the equipment away from the battery. This method reduces the risk of sparks near the battery, which can be dangerous.
It is also important to regularly inspect the battery charging lines for any signs of wear or damage. Damaged cables or clamps can increase the risk of electrical accidents. If any defects are found, replace the components immediately to maintain the integrity of the charging system.
By following these guidelines and handling battery charging lines with care, you can significantly reduce the risk of accidents and ensure a safer working environment. Proper training and adherence to safety protocols are essential for anyone involved in battery maintenance and charging operations.
Protective Gear for Battery Maintenance
When it comes to battery maintenance, using the appropriate protective gear is paramount to ensure safety and minimize potential hazards. Proper protective equipment serves as a crucial barrier against chemical exposure, electrical shocks, and physical injuries. Among the essential items, goggles and gloves stand out as indispensable tools. Each piece of gear offers unique benefits tailored to the specific risks associated with handling batteries.
Goggles are vital in protecting the eyes from harmful chemicals, such as acid splashes that can occur during battery maintenance. Eye protection is not only a precaution against splashes but also against flying debris that may result from the handling or accidental damage of batteries. It's important to select goggles that provide a snug fit and are made from materials resistant to chemical corrosion, ensuring both comfort and durability.
Equally important are gloves, which shield the hands from contact with corrosive materials and electrical hazards. The right pair of gloves can prevent burns, cuts, and chemical absorption. When selecting gloves, it's advisable to opt for those made of nitrile or other chemical-resistant materials. These materials offer superior protection against acids commonly found in batteries while maintaining flexibility for precise handling tasks.
In addition to goggles and gloves, other protective gear such as aprons, face shields, and insulated tools can further enhance safety measures. Aprons made of rubber or PVC provide additional defense against spills and splashes, while face shields offer extended coverage for the face and neck. Insulated tools, on the other hand, reduce the risk of electrical shocks by preventing direct contact with live circuits.
Choosing the right protective gear involves considering the specific requirements of the maintenance task and the type of battery being handled. Investing in high-quality, certified protective equipment not only ensures compliance with safety standards but also promotes a culture of safety within the workplace. Ultimately, wearing the appropriate protective gear during battery maintenance activities significantly reduces the risk of accidents and promotes a safer working environment for all involved.
Expert Consultation for Battery Use and Maintenance
In the realm of electronic systems and equipment maintenance, the significance of proper battery handling cannot be overstated. Seeking expert advice for any questions related to battery use and maintenance is crucial in ensuring safety, performance, and longevity. Professional guidance can provide invaluable insights into the correct procedures and best practices, thereby preventing potential mishaps and extending the operational life of batteries.
For any uncertainties or specific inquiries, contacting the company's sales or after-sales personnel is highly recommended. These professionals are equipped with the requisite knowledge and experience to address a wide range of issues, from selection and installation to maintenance and troubleshooting. They can offer tailored solutions based on the unique requirements of your equipment and operational environment.
Expert consultation is particularly beneficial in addressing complex scenarios such as identifying the appropriate type of battery for specialized equipment, understanding the nuances of battery chemistry, and implementing preventive maintenance strategies. Additionally, professional advice can assist in diagnosing and resolving issues like unexpected battery drain, overheating, and compatibility concerns.
Moreover, engaging with experts can provide clarity on regulatory compliance and safety standards, ensuring that your practices align with industry norms and legal requirements. This proactive approach not only safeguards your equipment but also enhances overall operational efficiency.
In essence, leveraging the expertise of qualified personnel mitigates risks associated with battery use and maintenance, fostering a safer and more reliable operational framework. Whether you are faced with routine maintenance tasks or complex technical challenges, the support of knowledgeable professionals is indispensable in navigating the intricacies of battery management.
Conclusion: Best Practices for Battery Safety
In summary, ensuring battery safety in electronic systems and equipment maintenance is paramount. The comprehensive measures discussed throughout this blog post highlight the critical precautions necessary to prevent accidents and optimize battery performance. By adhering to these best practices, users can significantly mitigate risks associated with battery mishandling, such as short circuits, overheating, and potential explosions.
First and foremost, proper storage and handling are crucial. Batteries should be kept in cool, dry environments, away from direct sunlight, and stored in non-conductive containers. Regular inspection and maintenance are essential to identify any signs of damage, corrosion, or leakage early. Ensuring that batteries are compatible with the devices they power and using appropriate chargers are also vital steps that cannot be overlooked.
Moreover, understanding the specific requirements and limitations of different battery types can further enhance safety. For instance, lithium-ion batteries demand particular attention due to their sensitivity to temperature and voltage variations. Employing protective circuits and battery management systems can safeguard against overcharging, deep discharging, and other hazardous conditions.
Educating oneself and others about the potential dangers and safe handling practices of batteries is another critical aspect. This includes familiarizing with safety labels, manufacturer guidelines, and disposal procedures. Importantly, in situations where uncertainty arises, seeking professional assistance is strongly encouraged to avoid compromising safety.
Ultimately, prioritizing battery safety not only extends the lifespan of electronic equipment but also ensures the well-being of users. The outlined precautions serve as a foundational guide to fostering a safe and efficient environment for battery usage. By integrating these practices into routine maintenance and operation, individuals can contribute to a safer, more reliable landscape for electronic systems and equipment.