Precautions During Transportation: Safe Loading and Unloading of Mini-Excavators
7/13/20247 min read
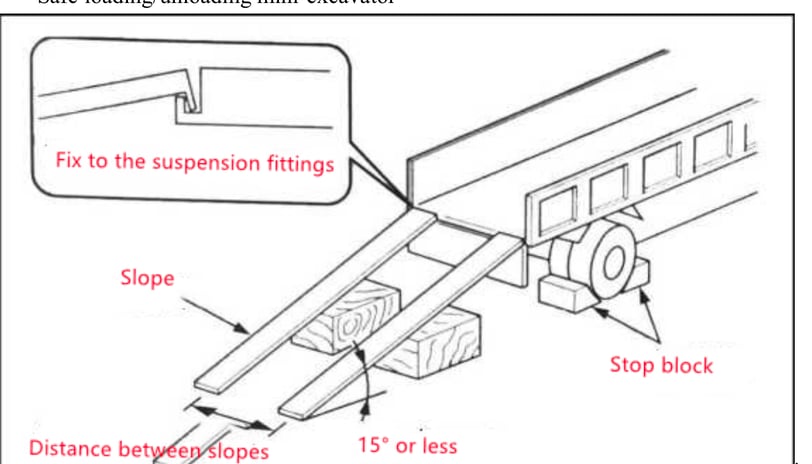

Introduction to Mini-Excavator Transportation Safety
Transporting mini-excavators requires meticulous attention to safety protocols to avert potential hazards. Mini-excavators, though compact, possess substantial weight and power, making them susceptible to accidents such as overturning or falling during loading and unloading processes. The significance of adhering to safety precautions cannot be overstated, as negligence can lead to severe injuries or fatalities for operators and nearby personnel.
The process of loading and unloading mini-excavators involves several critical steps, each fraught with its own set of risks. The stability of the excavator must be maintained at all times to prevent tipping. Furthermore, the alignment of loading ramps, the condition of securing chains and straps, and the terrain on which the transport takes place, all contribute to the overall safety of the operation. Without proper measures, even minor oversights can lead to catastrophic outcomes.
Considering the complexity of these tasks, it is imperative to follow established guidelines and best practices. Operators must be adequately trained in handling mini-excavators and familiar with the specific safety protocols related to their transportation. Additionally, regular equipment inspections and maintenance are essential to ensure that all components are in optimal working condition before any transportation activity.
By implementing stringent safety measures, the risks associated with the transportation of mini-excavators can be significantly mitigated. The emphasis on safety not only protects the individuals directly involved but also safeguards the surrounding environment from potential damage. Comprehensive safety protocols serve as a cornerstone for efficient and secure transportation operations, underscoring the importance of vigilance and preparedness in the handling of mini-excavators.
Choosing the Right Location for Loading and Unloading
When it comes to the safe transportation of mini-excavators, selecting the proper location for loading and unloading is crucial. The primary consideration should be ensuring the ground is solid and flat. A stable surface not only facilitates smoother operations but significantly reduces the risk of accidents. Loose gravel, uneven terrain, or soft soil can jeopardize the stability of the mini-excavator, leading to potential tipping or sliding, which could result in severe damage or injury.
Additionally, maintaining a sufficient distance from the road shoulder and other potential hazards is vital. The proximity to traffic, steep slopes, or water bodies can introduce unnecessary risks. It is advisable to keep the loading and unloading activities away from these dangers to ensure the safety of both the operators and the equipment. A clear area also provides better visibility, allowing the operators to maneuver the machinery with precision and confidence.
The impact of an uneven surface on the stability of the mini-excavator cannot be overstated. Uneven ground may cause the mini-excavator to tilt or shift unexpectedly during loading or unloading. This instability can lead to the machinery toppling over, posing significant risks to the safety of the operator and bystanders, as well as causing potential damage to the equipment. Therefore, it is imperative to inspect the ground conditions thoroughly before commencing any loading or unloading procedures.
In conclusion, choosing the right location for loading and unloading mini-excavators plays a pivotal role in ensuring safe operations. Prioritizing solid, flat ground, maintaining a safe distance from hazards, and being mindful of the equipment's stability can prevent accidents and ensure a smooth and efficient transportation process. By adhering to these precautions, operators can mitigate risks and ensure the safety and longevity of their machinery.
Setting Up a Safe Ramp
When transporting mini-excavators, ensuring the safety of the ramp used for loading and unloading is crucial. A proper ramp must possess sufficient strength and size to support the weight of the mini-excavator and any additional equipment. The ramp's construction should be robust, using high-quality materials to prevent bending or breaking under load stress.
One of the critical aspects of ramp setup is its slope. The incline of the ramp should not exceed 15 degrees. A steeper slope increases the risk of the mini-excavator slipping or tipping over during loading and unloading, which can lead to severe accidents and equipment damage. Therefore, maintaining a gentle and manageable slope is essential for operational safety.
Excessive downward curvature of the ramp poses another significant danger. A ramp with too much downward curvature can cause instability, making it difficult to control the mini-excavator as it moves up or down the ramp. This curvature can also lead to uneven weight distribution, increasing the likelihood of the ramp failing under pressure.
To mitigate these risks, implementing additional support measures is advisable. Using struts or cushion blocks can provide extra stability and prevent the ramp from bowing or shifting during use. These supports should be strategically placed to bear the weight evenly and maintain the ramp's structural integrity.
Moreover, the ramp must be securely fastened to the truck compartment. Proper securing mechanisms, such as locking pins or chains, should be used to anchor the ramp firmly, preventing any movement during the loading and unloading process. This ensures that the ramp remains in place, providing a safe and reliable pathway for the mini-excavator.
In conclusion, setting up a safe ramp involves careful consideration of its strength, size, slope, curvature, and securing methods. By adhering to these guidelines, operators can significantly reduce the risks associated with transporting mini-excavators, promoting a safer and more efficient loading and unloading process.
Maintaining Clean Loading Surfaces
Ensuring the loading surfaces are clean is a critical aspect of safely transporting mini-excavators. A truck compartment and loading surface must be meticulously maintained, free from oil, sand, ice, snow, and other foreign materials. These substances can significantly compromise the safety of the loading and unloading process. When such contaminants are present, they create a high risk for sideslip, which can lead to accidents and equipment damage.
Oil and grease are particularly hazardous as they reduce the friction between the mini-excavator's tracks and the loading surface. This reduction in traction can cause the equipment to slide unexpectedly during the loading or unloading process, endangering both the operator and the machinery. Similarly, sand and loose gravel can create an uneven and unstable surface, posing a threat to the stability of the mini-excavator as it is maneuvered onto or off the truck.
In colder climates, ice and snow are frequent challenges. These elements can make the loading surface slippery and unpredictable. Ice, in particular, can form a thin, almost invisible layer that drastically reduces traction, increasing the likelihood of sideslip. Snow, while more visible, can also conceal other hazards and contribute to instability.
Maintaining a clean caterpillar band on the mini-excavator is equally crucial. Debris lodged in the tracks can impair the machinery's ability to grip the loading surface properly. Therefore, it is essential to regularly inspect and clean the caterpillar band, removing any accumulated dirt, stones, or other detritus.
By prioritizing the cleanliness of both the loading surfaces and the mini-excavator's tracks, operators can significantly reduce the risk of accidents. This practice ensures a safer environment for the transportation of heavy machinery, preserving the integrity of the equipment and the safety of the personnel involved.
Securing the Mini-Excavator
Ensuring the safety of both the mini-excavator and the personnel involved in its transportation begins with adequately securing the transport vehicle. Properly wedging the wheels of the transport vehicle is a critical first step. Position wheel chocks in front of and behind the wheels to prevent any unintended movement during loading and unloading. Make sure the chocks are made of durable material and are appropriate for the vehicle's weight and wheel size.
Beyond wheel chocks, additional securing devices are indispensable for maintaining the stability of the mini-excavator. Chains and straps are commonly used to anchor the mini-excavator effectively. Utilize heavy-duty chains to create multiple anchor points around the mini-excavator. Ensure these chains are rated for the weight of the equipment and are free of any defects or wear that could compromise their strength. Secure the chains to the transport vehicle's designated tie-down points, which are designed to handle significant loads.
Straps can serve as supplementary securing devices. Use straps that are specifically designed for heavy equipment, with ratchet mechanisms to ensure they are tightly fastened. Position the straps over and around the mini-excavator, ensuring that all critical points of the equipment are secured. The combination of chains and straps provides an added layer of security, significantly reducing the risk of movement during transit.
Regular inspections throughout the transportation process are paramount. Before departure, double-check all securing devices to confirm they are correctly installed and tensioned. During transit, periodic stops to inspect the chains and straps will ensure that they remain tight and have not loosened due to vibrations or movement. A vigilant approach to securing the mini-excavator guarantees not only the safe delivery of the equipment but also the safety of everyone involved in the transportation process.
Final Safety Checks and Operator Training
Ensuring the safe loading and unloading of mini-excavators is paramount to preventing accidents and equipment damage. Before initiating any loading or unloading process, conducting thorough final safety checks is essential. These checks serve as the last line of defense in identifying any potential issues that could jeopardize safety.
Key areas to inspect include the integrity of the loading ramps, the stability of the mini-excavator, and the condition of the transport vehicle. The loading ramps should be inspected for any signs of wear or damage that could compromise their strength. It is equally important to confirm that the ramps are securely attached to the vehicle to prevent any movement during the loading or unloading process.
The stability of the mini-excavator should also be verified. This involves checking the tracks or wheels for any debris that could affect traction, ensuring that the excavator is positioned on level ground, and confirming that all safety locks and brakes are engaged. Additionally, the transport vehicle should be inspected for any mechanical issues that could affect its stability or the effectiveness of its safety mechanisms.
Operator training is another crucial component in ensuring the safe handling of mini-excavators during transportation. Operators must be well-versed in the specific safety procedures related to loading and unloading. This includes understanding the correct techniques for maneuvering the mini-excavator onto and off the transport vehicle, as well as being aware of the potential hazards associated with the task.
Proper training should also cover emergency protocols, such as how to respond if the mini-excavator slips or if there is a sudden mechanical failure. By equipping operators with the knowledge and skills necessary to handle these situations, the risk of accidents can be significantly minimized.
In conclusion, performing final safety checks and ensuring that all operators are adequately trained are fundamental steps in safeguarding the transportation process of mini-excavators. These measures not only protect the operators but also preserve the integrity of the equipment and the transport vehicle.