Essential Sign-On Precautions for Mini-Excavator Operation
Essential Sign-On Precautions for Mini-Excavator Operation
7/27/20247 min read
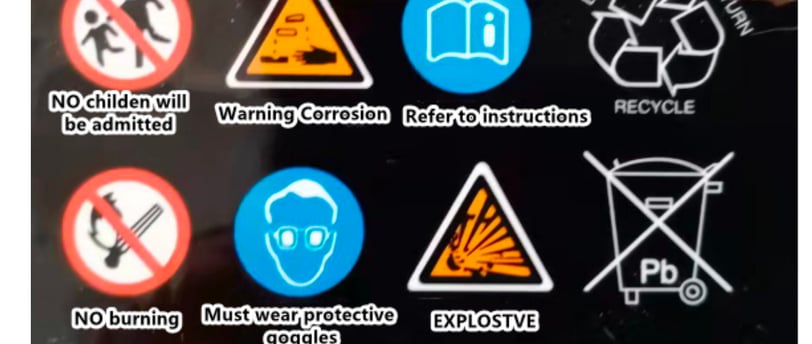
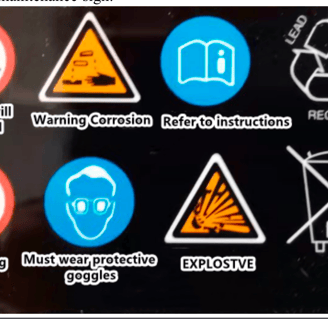
Understanding the Importance of Sign-On Precautions
In the realm of heavy machinery, particularly mini-excavators, the adherence to sign-on precautions is not merely a recommendation but a critical necessity. These precautions serve as the first line of defense in ensuring the safety of operators and the longevity of the equipment. Neglecting these essential steps can lead to catastrophic outcomes, including severe injuries, fatalities, and substantial damage to the mini-excavator itself.
Sign-on precautions are designed to address and mitigate the inherent risks associated with operating heavy machinery. They encompass a range of preparatory actions that operators must undertake before beginning any task, from inspecting the equipment for any signs of wear and tear to verifying that all safety mechanisms are functional. These precautions also include the necessity of reading and comprehensively understanding the operation manual. This document contains critical information about the machine’s capabilities, limitations, and specific operational guidelines that are indispensable for safe operation.
Ignoring these precautions can result in dire consequences. For instance, an operator who fails to check the hydraulic systems may find themselves in a situation where the mini-excavator's arm becomes uncontrollable, posing severe risks to both the operator and those in the vicinity. Similarly, neglecting to ensure that the ground is stable before operation can lead to tipping over, which can be fatal. Therefore, the importance of sign-on precautions cannot be overstated; they are a fundamental aspect of responsible mini-excavator operation.
Moreover, the operational manual serves as a comprehensive guide that equips operators with the knowledge necessary to handle the machine effectively and safely. It is crucial that operators not only read this manual but also fully understand its contents. Familiarity with the manual ensures that operators are well-informed about the mini-excavator's features and functions, enabling them to operate the machine within safe parameters and reducing the likelihood of accidents.
High-Risk Precautions: Preventing Death and Serious Injury
Operating a mini-excavator presents inherent risks that can lead to fatal or severe injuries if not properly managed. High-risk precautions are paramount to ensure the safety of operators and surrounding personnel. One of the most critical measures includes conducting thorough pre-operation checks. These checks involve inspecting the hydraulic systems, verifying the functionality of the safety features, and ensuring that all control mechanisms are responsive. Neglecting these inspections can result in catastrophic equipment failure.
Another significant aspect is the proper use of personal protective equipment (PPE). Operators must wear hard hats, high-visibility vests, steel-toe boots, and other relevant gear to mitigate injury risks. It's essential to be vigilant about environmental conditions, such as operating on uneven terrain or near overhead power lines, which can substantially increase the risk of accidents.
One common scenario where high-risk precautions are often neglected is during the loading and unloading of mini-excavators from trailers. This process requires meticulous attention as improper securing or unstable ground can easily lead to rollovers. Rollovers are among the most frequent causes of severe injuries and fatalities in mini-excavator operations. Hence, ensuring the ground's stability and using proper loading techniques are non-negotiable safety measures.
Case studies have shown the dire consequences of ignoring these precautions. For instance, a recent incident involved an operator who bypassed the pre-operation inspection protocol, leading to hydraulic failure during excavation. The equipment tipped, causing serious injury to the operator. Another case highlighted the failure to wear appropriate PPE, resulting in a worker sustaining head injuries from falling debris.
These examples underscore the gravity of adhering to high-risk precautions. By prioritizing these measures, operators can significantly reduce the likelihood of fatal and severe injuries, fostering a safer working environment.
Risk of Injury: Essential Safety Measures
Operating a mini-excavator entails a variety of risks, particularly the potential for non-fatal but serious injuries. To mitigate these risks, it is imperative to adhere to essential safety measures. A prevalent mistake among operators is the neglect of personal protective equipment (PPE). Wearing appropriate PPE, such as hard hats, high-visibility vests, gloves, and steel-toed boots, is crucial in safeguarding against injuries.
Another common oversight is improper training. Operators must receive comprehensive training, covering both theoretical knowledge and practical skills. This includes understanding the mini-excavator's controls, load limits, and the significance of stability. Additionally, operators should be familiar with the machine's safety features, such as emergency stop buttons and backup alarms.
Safe operation techniques are paramount. One critical aspect is maintaining a safe distance from the excavator’s moving parts. Operators should always be aware of their surroundings and ensure that no personnel are within the swing radius. Moreover, adhering to the manufacturer's guidelines regarding load limits and avoiding overloading the bucket can prevent tipping and other hazardous situations.
Proper communication on-site is also essential. Clear signals and hand gestures should be standardized and understood by all team members. This minimizes the risk of miscommunication, which can lead to accidents. Furthermore, regular maintenance checks of the mini-excavator are vital. Routine inspections for hydraulic leaks, tire pressure, and the integrity of attachments can prevent mechanical failures that might result in injuries.
Lastly, operators should be mindful of environmental conditions. Wet or uneven terrain can significantly affect the stability of the mini-excavator. Adjusting operations to accommodate these conditions, such as reducing speed and using stabilizers, can enhance safety. Adopting these precautionary measures not only promotes a safer working environment but also ensures the longevity and efficiency of the mini-excavator.
Preventing Equipment Damage and Failure
Ensuring the longevity and optimal performance of a mini-excavator requires adhering to specific precautions aimed at preventing damage and operational failures. Operators must be vigilant in their approach, as improper use or neglect can lead to substantial costs associated with repairs and extended downtime.
One critical aspect of preventing equipment damage is following the manufacturer's guidelines for operation. These guidelines detail the appropriate procedures for handling the machine, including load limits, operating speeds, and safe maneuvering techniques. Ignoring these specifications can result in overloading the equipment, leading to structural damage or mechanical failures. Regularly reviewing and adhering to these instructions is essential for the safe and efficient use of the mini-excavator.
Maintenance plays a pivotal role in preventing operational failures. Routine inspection and servicing of the mini-excavator should be carried out according to the manufacturer's maintenance schedule. This includes checking fluid levels, such as engine oil, hydraulic fluid, and coolant, to ensure they are within the recommended ranges. Additionally, inspecting the machine for signs of wear and tear, such as cracks, leaks, or frayed cables, can help identify potential issues before they escalate into major problems.
Another key precaution is keeping the mini-excavator clean. Dirt and debris can accumulate in critical areas such as the engine compartment, hydraulic system, and undercarriage, leading to blockages, overheating, or component failure. Regular cleaning not only enhances the machine's performance but also extends its lifespan. It is advisable to use appropriate cleaning tools and techniques to avoid causing damage during the cleaning process.
Furthermore, operators should be trained and experienced in using the mini-excavator. Proper training ensures that operators understand the machine's capabilities and limitations, reducing the risk of accidents and equipment misuse. Ongoing training and refresher courses can keep operators updated on best practices and new safety protocols.
By implementing these precautions—following manufacturer guidelines, maintaining regular inspections, keeping the equipment clean, and ensuring operator training—operators can significantly reduce the risk of equipment damage and failure, thereby ensuring the mini-excavator remains in optimal working condition for longer periods.
Supplementary Instructions for Optimal Use
To ensure the optimal use of a mini-excavator, it is imperative to adopt advanced operational techniques and adhere to routine maintenance practices. One of the key recommendations is to always conduct a pre-operation inspection. This involves checking fluid levels, examining hydraulic hoses for leaks, and ensuring that all safety devices are functional. By addressing potential issues before operating the mini-excavator, operators can prevent unexpected breakdowns and reduce the risk of accidents.
Another crucial aspect of optimal mini-excavator use is mastering the control system. Operators should familiarize themselves with the machine's controls to execute precise movements, which is particularly important in confined spaces. It is advisable to practice in a safe area before undertaking actual tasks. This not only enhances productivity but also minimizes wear and tear on the equipment.
Routine maintenance is vital for the longevity of mini-excavators. Regularly scheduled services, such as oil changes, filter replacements, and lubrication of moving parts, help in maintaining the machine's performance. Keeping a maintenance log can assist in tracking service intervals and identifying recurring issues that may require attention.
Additionally, it is beneficial to follow specific operational tips that can extend the life of a mini-excavator. For example, avoiding overloading the bucket, operating at a steady pace, and using the correct attachment for the job can significantly reduce strain on the machine. It is also recommended to shut down the engine when the equipment is not in use to conserve fuel and prevent unnecessary idling.
Finally, operators should stay updated with the latest advancements and training opportunities related to mini-excavator operation. Continuous learning and staying informed about new technologies can lead to more efficient and safer use of the equipment.
Comprehensive Understanding of the Operation Manual
A thorough comprehension of the operation manual is imperative for the safe and efficient use of a mini-excavator. The operation manual is a detailed guide that provides essential information about the machine's features, functions, and safety protocols. Operators should read the manual meticulously to familiarize themselves with the specific model of the mini-excavator they will be using. This foundational knowledge not only enhances operational efficiency but also significantly mitigates the risk of accidents and equipment damage.
To navigate the manual effectively, operators should start with the table of contents, which offers a structured overview of the document. Key sections typically include safety instructions, machine controls, maintenance schedules, and troubleshooting guidelines. Paying close attention to the safety instructions is crucial, as these sections outline the necessary precautions to prevent injury and ensure safe operation. Understanding the machine controls section will provide operators with detailed insights into the functionalities of various controls and indicators, enabling them to handle the equipment with confidence.
Maintenance schedules are another critical aspect of the operation manual. Regular maintenance is vital for the longevity and optimal performance of the mini-excavator. The manual typically includes a checklist of maintenance tasks that should be performed at specific intervals, along with detailed procedures for each task. Adhering to these guidelines helps in early detection of potential issues, thereby reducing downtime and repair costs.
For any uncertainties or need for further clarification, operators should not hesitate to seek additional assistance. This can be done by consulting the manufacturer’s customer support, reaching out to experienced colleagues, or attending training sessions provided by the equipment supplier. Many manufacturers also offer online resources such as instructional videos and FAQs, which can be invaluable for resolving specific queries.
In conclusion, a comprehensive understanding of the operation manual is a fundamental step in ensuring the safe and efficient use of mini-excavators. By diligently studying the manual and utilizing available resources for further assistance, operators can enhance their proficiency and contribute to a safer working environment.