Maximizing Efficiency with Mini Excavators: Maintenance
6/26/20247 min read
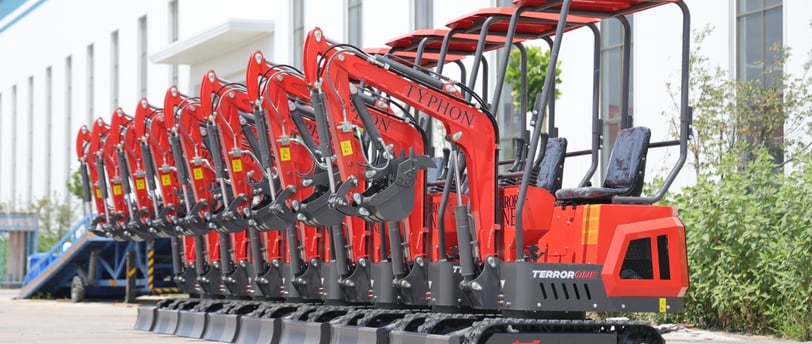
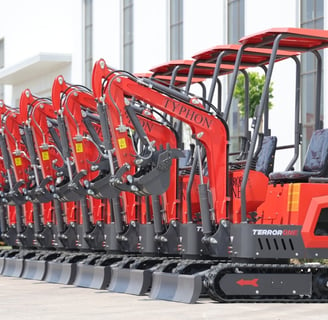
Introduction to Regular Maintenance
Regular inspection and maintenance of mini excavators are crucial for ensuring the longevity and efficiency of these versatile machines. By conducting routine checks, operators can prevent unexpected breakdowns, which not only cause costly downtime but can also lead to expensive repairs. Proper maintenance practices are essential for extending the life of the equipment and ensuring it operates at peak performance.
Mini excavators are complex machines with several interdependent systems that require regular attention. Key areas that should be inspected and maintained include the hydraulic system, engine, and tracks. The hydraulic system, which powers the excavator's movements, must be regularly checked for leaks, worn hoses, and proper fluid levels. Neglecting the hydraulic system can result in decreased performance and potential system failure.
The engine is another critical component that demands regular maintenance. Routine engine checks should include inspecting the oil levels, air filters, and fuel system. Ensuring the engine is in good condition helps maintain operational efficiency and prevents unexpected power losses. Regular oil changes and air filter replacements are simple yet effective measures to keep the engine running smoothly.
The tracks, which provide the mini excavator with mobility, also require periodic inspection. Operators should check for wear and tear, proper tension, and alignment. Maintaining the tracks in good condition ensures the machine can maneuver effectively across various terrains without causing undue stress on other components.
In summary, regular inspection and maintenance of mini excavators are essential for preventing breakdowns, extending equipment life, and maintaining operational efficiency. By focusing on key areas such as the hydraulic system, engine, and tracks, operators can ensure their mini excavators remain in optimal condition, ready to tackle any task with reliability and precision.
Hydraulic System Maintenance
The hydraulic system is a pivotal component in the operation of mini excavators, underpinning their functionality and efficiency. Ensuring regular and thorough maintenance of this system is imperative to avoid costly downtimes and prolong the lifespan of the equipment. One of the first steps in hydraulic system maintenance is to check for leaks. This involves meticulously inspecting all hydraulic connections, fittings, and joints for any signs of oil leakage. Small leaks can escalate into significant issues if not addressed promptly.
Another crucial task is the inspection of hydraulic hoses. Over time, these hoses can become worn or damaged due to constant pressure and movement. Look for signs of wear and tear, such as cracks, bulges, or abrasions. Replacing compromised hoses is essential to maintain the integrity of the hydraulic system and prevent potential failures.
Maintaining proper fluid levels is equally important. Hydraulic fluid plays a vital role in the smooth operation of the system, acting as a lubricant and coolant. Regularly check the hydraulic fluid levels and top up as necessary, ensuring the fluid is clean and free from contaminants. Using the manufacturer’s recommended hydraulic oil type and grade is crucial for optimal performance.
Replacing hydraulic oil and filters should be done based on usage patterns, particularly when the mini excavator is fitted with hydraulic front-end working devices like breaking hammers. These tools can accelerate the degradation of hydraulic oil, necessitating more frequent changes. Follow the manufacturer’s guidelines for oil and filter replacement intervals, and always use high-quality filters to maintain system cleanliness.
In summary, a well-maintained hydraulic system ensures the mini excavator operates efficiently and reliably. By regularly checking for leaks, inspecting hoses, maintaining fluid levels, and timely replacing oil and filters, operators can significantly enhance the operational longevity of their equipment.
Engine and Fluid Checks
Maintaining the engine of a mini excavator is crucial for its optimal performance and longevity. Regular engine and fluid checks are essential tasks that should not be overlooked. One of the primary components of engine maintenance is the engine oil. It is advisable to check the engine oil level daily before starting the machine. The oil should be replaced after every 250 hours of operation or as specified in the manufacturer’s manual. Using the correct grade of oil is vital to ensure the engine runs smoothly and efficiently.
Coolant levels are another critical aspect of engine maintenance. The coolant should be checked weekly to ensure it is at the appropriate level. Adequate coolant levels help prevent the engine from overheating and ensure consistent performance. It is recommended to replace the coolant every 1,000 hours or once a year, whichever comes first. Always use the coolant type specified by the manufacturer to avoid any compatibility issues.
Fuel filters play a significant role in maintaining engine efficiency. Clogged or dirty fuel filters can cause engine performance issues and reduce fuel efficiency. Therefore, it is important to inspect and replace fuel filters regularly. Fuel filters should be checked and replaced every 500 hours of operation to ensure the fuel system remains clean and free of contaminants.
Air filters are also essential in preventing engine damage. Dust and debris can accumulate in the air filters, restricting airflow to the engine and reducing its performance. Inspect the air filter daily and clean it as necessary. Replace the air filter every 250 hours or sooner if it appears excessively dirty or damaged. A clean air filter ensures that the engine receives adequate airflow, promoting efficient combustion and performance.
By adhering to these guidelines and maintaining a consistent schedule for engine and fluid checks, mini excavator operators can significantly enhance the machine's performance and extend its lifespan. Regular maintenance not only prevents costly repairs but also ensures that the mini excavator operates at its best, providing reliable service over time.
Track and Undercarriage Inspection
The track and undercarriage inspection of a mini excavator is a critical component of its regular maintenance routine. Proper inspection ensures that the machine remains stable and maneuverable, ultimately enhancing its operational efficiency and longevity.
Begin the inspection process by examining the track tension. Proper track tension is vital to prevent slippage and undue wear on the tracks and other components. To check the track tension, refer to the operator's manual for the recommended specifications. Typically, the track sag should be measured between the carrier rollers and the track shoes. If the sag is outside the recommended range, adjust the track tension accordingly. This adjustment can usually be done using a grease gun to add or release grease from the tensioning cylinder.
Next, inspect the rollers and idlers. Rollers are responsible for supporting the weight of the mini excavator and ensuring smooth track movement, while idlers help guide the tracks and maintain tension. Check for signs of wear, such as flat spots, cracks, or excessive play. Pay attention to the condition of the seals as well; damaged seals can lead to contamination and premature wear. Replace any worn or damaged rollers and idlers to maintain optimal performance.
Additionally, look for signs of wear or damage on the tracks themselves. This includes checking for missing or damaged track shoes, uneven wear patterns, and cracks. Addressing these issues promptly can prevent further damage and costly repairs. Regularly cleaning the tracks and undercarriage to remove debris, mud, and rocks can also prevent accelerated wear and maintain the excavator's maneuverability.
Proper maintenance of the tracks and undercarriage not only enhances the stability and maneuverability of the mini excavator but also extends the lifespan of these critical components. By incorporating these inspection steps into your regular maintenance routine, you can ensure that your mini excavator operates reliably and efficiently.
Electrical System and Battery Maintenance
Maintaining the electrical system and battery of a mini excavator is critical for ensuring its reliable operation. A well-kept electrical system not only prevents unnecessary downtime but also extends the lifespan of the equipment. To begin with, inspecting electrical connections regularly is essential. Loose or corroded connections can lead to poor performance or complete failure of the electrical components. Regularly checking these connections and ensuring they are tight and free from corrosion can mitigate potential issues.
Another vital aspect of electrical system maintenance is ensuring the battery is properly charged. A fully charged battery supports the efficient operation of the mini excavator, especially during colder months when starting can be problematic. Using a multimeter, operators can check the battery voltage and ensure it remains within the optimal range. If the voltage is consistently low, it may be time to replace the battery or investigate further electrical issues.
Cleaning battery terminals is another crucial maintenance task. Over time, battery terminals can accumulate dirt and corrosion, which can impede electrical conductivity. Regular cleaning of the terminals with a mixture of baking soda and water, followed by a thorough rinsing and drying, can prevent these issues. Applying a thin layer of petroleum jelly after cleaning can also help protect the terminals from future corrosion.
Neglecting the electrical system of a mini excavator can lead to various problems, including starting difficulties and operational failures. For example, a weak or dead battery can prevent the excavator from starting, causing delays and additional costs. Furthermore, faulty electrical connections can result in intermittent power loss, affecting the machine's performance and safety.
By adhering to these maintenance tips, operators can ensure that their mini excavator's electrical system remains in optimal condition. Regular inspections, proper charging, and clean battery terminals contribute significantly to the equipment's reliability and efficiency.
Safety Checks and Operator Training
Conducting regular safety checks is paramount to ensuring that mini excavators are safe to operate. A systematic approach to inspecting safety features can prevent accidents and enhance the longevity of the equipment. Operators should start by examining the lights, ensuring that all headlights, tail lights, and indicator lights function correctly. This is crucial for visibility, especially in low-light conditions or during night operations.
Equally important is the inspection of alarms and warning systems. Audible alarms should be tested to confirm they are working properly, as these systems alert operators and nearby personnel to potential hazards. Emergency stop buttons must be checked for accessibility and functionality, as they are vital in halting the machine swiftly in case of an emergency.
Other essential safety checks include inspecting the condition of the seat belt, verifying the integrity of the rollover protective structure (ROPS), and ensuring that all safety decals and instructions are clearly visible and legible. A thorough examination of hydraulic hoses and connections for leaks or wear can also prevent mechanical failures that could lead to unsafe operating conditions.
In addition to regular safety inspections, operator training plays a crucial role in maintaining the equipment and ensuring safe operation. Well-trained operators are more likely to adhere to safety protocols and perform routine maintenance checks. Initial training should cover the basics of operating the mini excavator, understanding its controls, and recognizing potential hazards.
However, training should not be a one-time event. Periodic refresher courses are recommended to keep operators updated on the latest safety practices and technological advancements. These courses can reinforce safe operating procedures and introduce new techniques for efficient and secure equipment use. By investing in continuous operator education, companies can significantly reduce the risk of accidents and improve the overall performance of their mini excavators.