Essential Precautions for Safe Operation of Mini-Excavators
6/25/20247 min read
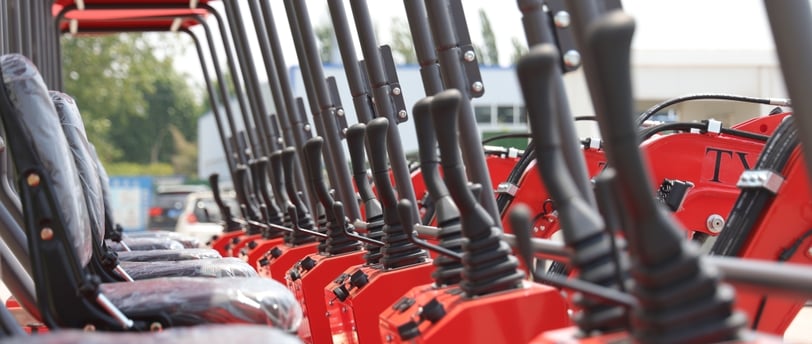
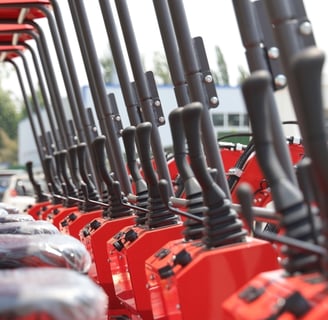
Ensure Good Line of Sight
Operating a mini-excavator with a clear line of sight is crucial for both safety and efficiency. Ensuring that the operator has an unobstructed view of the work area can significantly reduce the risk of accidents and improve operational precision. Inadequate visibility can lead to mishaps, which could potentially endanger the operator and others on the site.
When working in dark or poorly lit environments, it is imperative to utilize the work lights and headlights of the mini-excavator. These built-in lighting systems are designed to illuminate the immediate working area, providing better visibility and helping the operator to identify any obstacles or hazards. However, there are instances where the built-in lighting might not be sufficient, especially in expansive or exceptionally dark environments.
In such scenarios, the installation of additional lighting is recommended. Portable work lights, LED floodlights, or tower lights can be strategically placed around the working area to enhance visibility. These additional light sources should be positioned in a manner that eliminates shadows and ensures comprehensive illumination of the site. This approach not only aids in preventing accidents but also contributes to the overall efficiency of the operation by allowing the operator to work with greater accuracy.
Moreover, operators should be trained to regularly inspect and maintain the lighting systems of the mini-excavator. Ensuring that all lights are functioning correctly and replacing any faulty bulbs promptly can prevent unexpected visibility issues. In addition, operators must be aware of and comply with any site-specific lighting requirements or regulations to uphold safety standards.
By prioritizing a clear line of sight and employing appropriate lighting solutions, the risks associated with operating mini-excavators can be substantially mitigated. This practice not only safeguards the well-being of the operator but also contributes to the smooth and efficient execution of excavation tasks.
Handling Poor Visibility Due to Bad Weather
Weather conditions such as fog, snow, rain, or haze can severely impair visibility, making the operation of mini-excavators significantly more hazardous. In these scenarios, it is imperative to cease operation until visibility improves. The risk of accidents and equipment damage is heightened when visibility is compromised, thereby endangering both the operator and the surrounding environment.
Operators must prioritize safety above all else. Continuing to operate a mini-excavator under poor visibility can lead to serious consequences, including collisions with unseen obstacles, damage to the machinery, or even injury to the operator or nearby personnel. It is advisable to wait for weather conditions to improve before resuming work to mitigate these risks.
During periods of poor visibility, operators should also take additional precautions to ensure that the mini-excavator is secured and parked in a safe location. This prevents accidental movement or sliding, especially in slippery conditions caused by rain or snow. Proper use of lighting and signaling devices can also enhance visibility to some extent, but these measures should not substitute the necessity to halt operations when visibility is critically low.
Furthermore, operators should remain vigilant of weather forecasts and be prepared to adjust their schedules accordingly. Awareness of impending adverse weather conditions can enable better planning and minimize downtime while ensuring safety. Employers must also provide adequate training to operators on how to handle equipment during varying weather conditions and emphasize the importance of ceasing operations when visibility is compromised.
Ultimately, the safe operation of mini-excavators in poor visibility hinges on the operator's judgment and adherence to safety protocols. By taking these precautions, the risk of accidents and equipment damage can be significantly reduced, ensuring a safer work environment for all involved.
Prohibition of Carrying People
Adhering to safety regulations is paramount when operating mini-excavators, and one critical rule is the prohibition of carrying people on any part of the machine during operation or while it is in motion. This includes standing or sitting on the tracks, bucket, or any other component of the mini-excavator. Such practices pose significant risks and can lead to severe injuries or even fatalities.
The design of mini-excavators is focused on performing excavation tasks efficiently and safely, with specific seating and control areas designated for operators. These machines are not equipped to safely accommodate passengers in any capacity. Allowing individuals to ride on parts of the mini-excavator can disrupt the balance and operation of the machine, increasing the likelihood of accidents.
Operators have a responsibility to ensure that only authorized personnel are present in the operator cabin, the designated area built for safety and control. This cabin is equipped with necessary safety features such as seat belts, roll-over protection structures (ROPS), and other critical controls that are essential for secure operation. Unauthorized individuals on the machine can distract the operator, impair their ability to manage the equipment, and escalate the risk of mishaps.
Moreover, standing on the tracks or bucket of a mini-excavator can result in falls from heights, crushing injuries, or being struck by moving parts. The dynamic nature of excavation work means that the machine's components are frequently in motion, and any unplanned movement can have catastrophic consequences for individuals not safely positioned in the operator cabin.
In conclusion, it is crucial to enforce the guideline of prohibiting the carrying of people on mini-excavators. Operators must be vigilant in maintaining this rule to ensure the safety of all personnel on site. Adhering to this safety measure not only protects individuals from harm but also promotes a safer and more efficient working environment.
Understanding Performance Limits
Each mini-excavator is engineered with distinct performance limits and operational ranges, tailored to specific tasks and environments. Operators must be acutely aware of these parameters to ensure safe and efficient operation. Knowing the machine's capabilities helps in avoiding tasks that might exceed its design and compromise safety. Overloading or pushing a mini-excavator beyond its intended range can result in severe mechanical failures, increased wear and tear, and significant safety hazards.
Manufacturers provide comprehensive guidelines and specifications for their equipment. These guidelines include weight limits, operational angles, and safe working loads. Adhering to these specifications is crucial in preventing undue stress on the machine's components, which can lead to costly repairs and downtime. Furthermore, understanding the performance limits helps in planning tasks more effectively, ensuring that the mini-excavator is used within its optimal capacity.
Overloading is a common issue that arises when operators attempt to use the mini-excavator for tasks better suited to larger machines. This not only risks the integrity of the equipment but also endangers the operator and surrounding personnel. For instance, lifting loads heavier than the specified limit can lead to tipping or loss of control, which are significant safety risks. Therefore, operators must resist the temptation to push the machine beyond its limits, even if it seems capable of handling the extra load.
In addition to weight limits, operators should be mindful of operational angles and terrain. Mini-excavators are designed to function optimally on certain gradients and surfaces. Operating on steep slopes or uneven terrain beyond the recommended specifications can destabilize the machine, leading to accidents. Regularly reviewing the manufacturer’s manual and undergoing proper training can reinforce this understanding and promote safer operational practices.
Ultimately, respecting the performance limits of mini-excavators is integral to ensuring their longevity and the safety of their operation. By adhering to the manufacturer’s guidelines and avoiding overloading, operators can maintain the machine's integrity and create a safer work environment.
```htmlRegular Maintenance and Inspections
Routine maintenance and inspections are critical in ensuring the safe and efficient operation of mini-excavators. Daily checks should be a fundamental practice for operators, focusing on identifying any signs of wear and tear that may compromise the equipment's performance. Key areas to inspect include the integrity of hydraulic hoses, the condition of tracks or tires, and the proper functioning of the machine's various components.
Fluid levels also warrant close attention. Checking engine oil, hydraulic fluid, coolant, and fuel levels before starting the mini-excavator can prevent operational issues and extend the machine's lifespan. It is advisable to follow the manufacturer's guidelines on fluid types and replacement intervals to maintain optimal performance.
Equally important are the lights and safety features of the mini-excavator. Ensuring that all lights, including work and warning lights, are operational helps maintain visibility and safety on the job site. Safety features, such as seat belts, alarms, and emergency shut-off mechanisms, should be tested regularly to confirm they are functioning correctly.
Regular servicing as per the manufacturer's recommended schedule is another essential aspect of maintenance. This includes more comprehensive checks and replacements that go beyond daily inspections, such as changing filters, lubricating moving parts, and calibrating controls. Adhering to these schedules can prevent unexpected breakdowns and contribute significantly to the longevity of the mini-excavator.
In summary, a systematic approach to regular maintenance and inspections not only ensures the safe operation of mini-excavators but also enhances their efficiency and durability. By integrating these practices into daily operations, operators can minimize downtime, reduce repair costs, and maintain a high standard of safety on the job site.
Training and Certification
Ensuring that mini-excavator operators receive proper training and certification is a cornerstone of safe operation. It is imperative that operators are thoroughly educated in the machine's operational controls, safety protocols, and emergency procedures. Comprehensive training programs should encompass both theoretical knowledge and hands-on experience to equip operators with the necessary skills to handle mini-excavators efficiently and safely.
Training should cover a variety of essential topics, including but not limited to, understanding the machine's control systems, recognizing and mitigating potential hazards, and adhering to established safety guidelines. Additionally, operators must be trained to perform pre-operational inspections to identify any faults or issues that could compromise safety. Familiarity with emergency shutdown procedures and first aid practices is also crucial in minimizing risks during unforeseen incidents.
As technology in mini-excavator design and operation continually evolves, it is essential for operators to engage in ongoing training programs. These programs should be aimed at keeping operators updated with the latest safety practices, technological advancements, and regulatory changes. Employers play a vital role in this process by facilitating access to continuous education and ensuring that all operators participate in regular refresher courses.
Certification is another critical aspect of operator preparedness. Employers must ensure that all mini-excavator operators hold valid certifications from recognized training institutions. This certification process typically involves rigorous testing and assessment to confirm an operator's competency. Regular re-certification is also necessary to ensure that operators maintain a high level of proficiency and stay abreast of new developments in the field.
By prioritizing proper training and certification, employers can significantly enhance the safety and efficiency of mini-excavator operations. Well-trained operators are not only more productive but also better equipped to prevent accidents and handle emergencies, thereby contributing to a safer work environment.